What You Need to Know About Concrete Repair
Concrete Repair Bismarck requires a level of skill and knowledge that goes beyond surface issues. It is important to understand the underlying cause of damage and how it affects structural performance and property function.
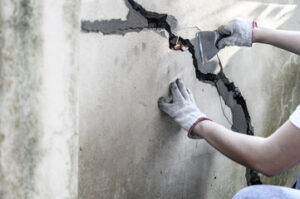
It’s also worth determining whether the problem is best repaired or replaced. Repairs are often quicker and cheaper, but replacement might be a better option if the damage compromises structural integrity.
Hydraulic cement is a type of cement that reacts with water to set and harden. This reaction creates calcium hydroxide as a byproduct and also prevents the cement from deteriorating in wet environments. This cement can be used to repair cracks, holes and leaks in concrete structures. It is also useful for dental applications, such as filling holes and repairing cracked teeth. This type of cement is typically mixed with other ingredients such as gypsum or sand to achieve the proper consistency for application. It is recommended that you read the manufacturer’s instructions before using this type of cement.
While hydraulic cement provides a quick solution to many basement leaks, it does not address the underlying issue. For permanent repairs, you may want to consider exterior waterproofing membranes that provide a barrier against moisture penetration. This type of waterproofing is not suitable for expansion joints, as they are designed to move and should be sealed with more flexible materials.
Non-hydraulic cement is a common and popular building material, but it requires dry conditions to cure and gain strength. This restriction makes it a poor choice for open construction sites, where weather conditions can be unpredictable. Hydraulic cement was developed to improve on this limitation, and it does so well that many builders now prefer it over non-hydraulic cement.
The best part about this type of cement is that it starts to set almost immediately, and can even be set while damp. This allows you to seal leaking cracks and gaps before they get worse, saving time and money. It is also easy to mix, and can be used in a variety of applications. This includes sealing cracks, floor-wall joints, and utility openings.
If you’re having trouble with a leak in your home, try using DRYLOK Fast Plug, a high-strength hydraulic cement that can be used to stop active leaks and seal leaky floors, walls, and basements. It is easy to apply and sets within three minutes. Just remember to wear eye protection, a dust mask, and gloves while working with this product. It’s important to mist the area periodically with water for 24 hours after completing your repair.
Bonding agents
A concrete bonding agent is an adhesive used to ensure the proper adhesion between layers of material in construction. This is essential in new construction and renovation projects. It improves the durability and efficiency of the final product. Bonding agents are also used to repair cracks and damaged concrete surfaces.
Concrete bonding agents are available in a variety of forms and are designed for various applications. Some are liquid and are mixed with water, cement, and sand to create a slurry that can be applied to the surface. Others are powdered and are mixed right before they are applied to the concrete. Both types of bonding agents offer excellent adhesion and resistance to corrosion, which is important in the construction industry.
To apply a concrete bonding agent, first clean the area thoroughly to remove any dirt or debris that could act as a bond breaker. Sweep the area or use a pressure washer to ensure that it is free of contaminants. Then, prepare the site by bringing it to saturated surface dry (SSD). This means that the surface is wet to the touch but has no standing water.
Once the concrete is cleaned, it’s time to apply the bonding agent. Liquid bonding agents are typically applied with a brush or trowel, while powdered bonding agents are often mixed before they are applied to the surface. Once the bonding agent is in place, it’s time to install the new concrete layer.
Concrete bonding products can be used to fill cracks, patch holes, and cover stains in both commercial and residential structures. They can also be used for seismic repairs and repairing corrosion in rebar and other structural steel. Using these products is an economical way to repair deteriorated concrete. The best type of concrete repair will depend on the severity of the damage and the desired outcome of the project. If you’re unsure what type of repair you need, consult a professional to determine the best solution. They can help you choose the right products and tools for your project. In addition, they can provide you with valuable information about the condition of your concrete and what repairs are necessary to keep it in good shape.
Prestressing steel
A high-strength steel element such as wire, bar or strand is used to impart prestressed forces to concrete. It must meet certain quality and safety requirements before it is used in a structure. For example, it must be free of oil, dirt, scale, pitting and excessive rust, although a light coating of rust is permitted. Mechanical property and dimensional tests should also be performed on the strand before it is used in construction. In addition, it should be free of any kinks or creases and have a smooth surface.
Prestressing is commonly used in large structures such as bridges and buildings, but it can be used in smaller projects as well. It is especially useful in areas that need to support heavy loads, such as floors and beams. This method of concrete repair is typically faster and more economical than conventional reinforcement methods.
Post-tensioning is a type of prestressing that works within concrete structures by placing steel “tendons” under tension before the concrete hardens. This process allows the concrete to support external service loads and stress without sacrificing its tensile strength. It is a common practice in commercial building construction, including multi-level parking garages.
Precast prestressed concrete is manufactured in a factory before it is delivered to the construction site and placed in place. This method reduces construction time on-site and eliminates the need to wait for concrete to cure. It also provides a cost-effective solution to complicated structural designs, and it increases the efficiency of the construction process.
Concrete crack repair is a common problem on many construction sites. It can be repaired with a variety of materials, such as epoxy injections or chemical grouting. Epoxy injections are a quick and affordable way to fill cracks in concrete, but they can’t be used for deep or wide cracks. Instead, these types of repairs are best for shallow cracks that are not yet extending to the opposite side of the slab.
Another popular type of crack repair is dry pack mortar, which is made with one part cement and two and a half parts sand. This mortar is quick-curing and can be used in vertical and overhead applications. It is an excellent choice for high-traffic areas and can be applied to bare or damp concrete surfaces.
Patching
The concrete at your home or business is constantly exposed to forces that can wear it down-rain, foot traffic, blazing sun. The good news is that it’s not impossible to repair these problems with a little time and effort. Patching is one way to do this, but it’s important to choose the right concrete patching product for your project. The first step is to clean the area and remove any loose material with a grinder like the Onfloor 16. Next, you’ll want to prepare the surface to receive your concrete patch. This is crucial for a successful concrete patch, and the best preparation tool is a power grinder with a diamond blade. Once the area is ready, you can mix and apply the patching product. Follow the manufacturer’s instructions for mixing and application to ensure that you get a smooth, durable result.
When it comes to structural concrete repairs, the most common method is the use of concrete patches and rebar. This method can be used on sidewalks, driveways, parking garages, and other concrete surfaces that have been damaged by weather or by traffic. The concrete patching process uses a flowable concrete product that can be applied with a trowel. It can also be pressed into place with a hammer or a vibratory broom. The patching material is a combination of cement and aggregates that can be mixed with water to create a thick paste.
If you’re patching a hole in a slab, it is essential to take steps to prevent further damage to the concrete. The best way to do this is by using a slurry mixture that contains bonding agents. The mixture should be mixed with a slurry mixer or a hand-held concrete mixer. The slurry should be mixed until it’s a smooth consistency.
For larger repairs, a vibratory screed or 3-m (10-ft) straightedge can be used to finish and texture the patch to match the surface profile of the surrounding pavement. The finished patch should be cured for 24 hours before foot traffic is allowed and 72 hours for vehicular traffic. Consider applying Sakrete Cure ‘N Seal or Concrete and Paver Sealer to the entire slab after 28 days to protect it from future damage.
Planning a Successful Kitchen Remodel
The kitchen is the heart of your home. It’s where you cook, eat, and gather with family and friends. A well-designed kitchen can also increase the value of your home.
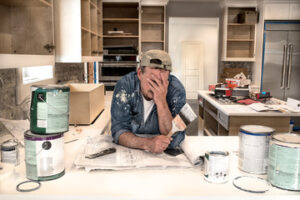
Before Kitchen Remodel in Denver begins, you need to understand the full scope of the project and its costs. Then set a budget that includes your needs and wants.
The kitchen is one of the most popular rooms to remodel and for good reason – it boosts resale value. It also serves as the heart of the home, so homeowners want it to be functional and look great. But it’s important to keep in mind that a kitchen remodel can be costly, especially if you don’t plan ahead or aren’t clear about what you want.
Some elements of a kitchen remodel are unavoidable, such as permitting fees, structural changes and electrical or plumbing upgrades. Other expenses may include new appliances, cabinet costs and labor. Experts suggest that you set aside 10%-20% of your budget for unexpected expenses. These can include unpleasant demolition discoveries (like water damage or outdated wiring) and unexpected extras (like hiring movers to move your stove).
To keep your kitchen remodeling costs down, prioritize your needs and wants. Work with a professional to create a list of the must-haves, and then compare that with your wish list to see what can be done without exceeding your budget. Avoid focusing on status-oriented features like granite countertops or Sub-Zero appliances, and instead opt for more affordable materials that will still look beautiful and last for years to come.
Lastly, don’t be afraid to use credit for your kitchen remodel. Many credit card companies offer 0% interest for a limited time, which can save you money on upfront costs and allow you to build up your credit score with consistent payments. Of course, be sure you can pay off the card within the 0% interest period to avoid hefty interest charges and to ensure that you don’t run out of cash during the project.
Design
Before you start tearing down walls and putting up new fixtures, work with your designer to develop a design plan. This is the best time to think through what features you want in your kitchen, including built-in appliances like steam ovens or wine fridges. It’s also a good time to consider energy-efficient options, which are not only better for the environment but can save you money in the long run.
A kitchen remodel involves a lot of choices, from cabinet color and flooring to countertop and backsplash. It’s important to weigh each option carefully, making sure it aligns with your goals and lifestyle. For example, if you’re planning on cooking more meals at home, it might be worthwhile to invest in a gas range with an extra-large oven. This will give you more room to cook and entertain.
During this stage, you’ll also determine how you want to use your kitchen on a daily basis. For example, are you looking to improve storage capacity or create a more efficient workflow? Understanding your goals can help you make smarter decisions that produce a more satisfying result.
Once you’ve mapped out your dream kitchen and fine-tuned the design, it’s time to turn your attention to permitting and approvals. This is a critical step that can prevent costly mistakes during construction. Whether you’re working with a general contractor or doing the work yourself, securing the proper permits can help you avoid expensive fines and keep your project on schedule.
Permits
While some changes are minor, others require a permit to ensure that the renovation complies with local building codes. The exact requirements can vary depending on the scope of work and your town’s regulations, but it is important to understand these requirements before hiring a contractor.
To get a permit, your hired professional will need to prepare and submit an application to the DOB with detailed blueprints of your kitchen remodeling project. The process may take a few weeks to complete. After approval, the DOB will send you guidelines and inspection schedules. It is important to follow these guidelines during construction to avoid fines and delays.
It is a good idea to consult with experts before starting your kitchen remodel to find out what types of changes or additions require a permit. Some projects do not need a permit, including sanding or repainting existing cabinets and installing new appliances in the same location. However, any electrical or plumbing work requires a permit. Also, it is a good idea to get a permit for any work that involves adding or removing walls.
If you do not have a permit for your kitchen remodeling, you will likely face legal complications. You may be required to tear down the unpermitted work and pay fines or repair any damage caused by the renovation. In addition, homeowners without permits cannot claim additional square footage on their home insurance policies. Furthermore, potential buyers will be wary of a home with unpermitted renovations and may doubt the quality of work. To avoid these complications, it is a good idea to consult with a design-build firm or licensed professionals before beginning your kitchen renovation.
Contractor
Kitchen remodeling requires a lot of work, and it’s best left to the professionals. A general contractor will manage the project and coordinate with subcontractors, ensuring that the job is completed in a timely manner. The contractor will also handle securing any required permits or inspections. This is especially important in NYC, where building codes are strict and violations can result in expensive fines.
The contractor will also provide recommendations for appliances and materials, as well as help you decide on a timeline. The kitchen renovation process will vary depending on the size and scope of the remodel, so it’s important to have a clear understanding of what you want from your new kitchen. For example, you might need to increase storage capacity or improve workflow efficiency. This will allow you to create a realistic budget and determine whether a remodel is the right option for your home.
One of the most difficult parts of kitchen renovation is removing existing elements and cleaning up debris. This can take weeks or even months, and it’s best to hire a general contractor. This will ensure that the process goes smoothly and minimizes disruption to your daily life.
When choosing a contractor, it’s important to consider their experience and reputation. Ask friends, family, and neighbors for referrals, and look for reviews online. Once you’ve narrowed your choices, schedule face-to-face meetings with each candidate to get a feel for their communication style and professionalism. It’s also a good idea to compare quotes from several contractors and make sure they are comparable. This will ensure that you get the best value for your money. A high-quality kitchen remodel is a worthwhile investment, but it’s important to stay within your budget.
Installation
Depending on the extent of your remodel, this phase can take a few days to several weeks. This is when new plumbing and electrical systems are installed. It also is the time to replace old, outdated, or damaged flooring and walls with fresh materials. It’s important to have licensed, insured professionals take care of this work because if anything goes wrong during installation, it could be dangerous and expensive.
While this is a noisy and messy process, it’s an essential step. Removing old cabinets, appliances, counters, and drywall is necessary to ensure that the space can be properly cleaned and prepared for new products to be installed. During this stage, the contractor will determine where the plumbing, electrical, and ventilation pipes will be placed, as well as upgrade old galvanized pipes to modern PEX piping. This is also the time to consider adding or moving outlets and light switches to accommodate new products, as well as change out old, outdated electrical wiring to current code standards.
If you’re planning a kitchen renovation, it’s helpful to get inspired by visiting Pinterest boards and home improvement websites. This will help you visualize your ideal kitchen layout and design, which you can show to the professionals working on the project.
Once the new plumbing and electrical systems are installed, the drywall can be installed. At this point, it’s important to remember that the walls must be insulated and weatherproofed. Then, countertops can be measured and fabricated, and cabinet hardware can be installed. Once the countertops are installed, a final inspection can be scheduled. During this phase, it’s possible to continue using your kitchen while the work is taking place, but you will likely have to eat out at restaurants or ask friends and family for meals until the remodel is complete.